Multifunctional Filling Machine for Filling 200L Paint Solvent
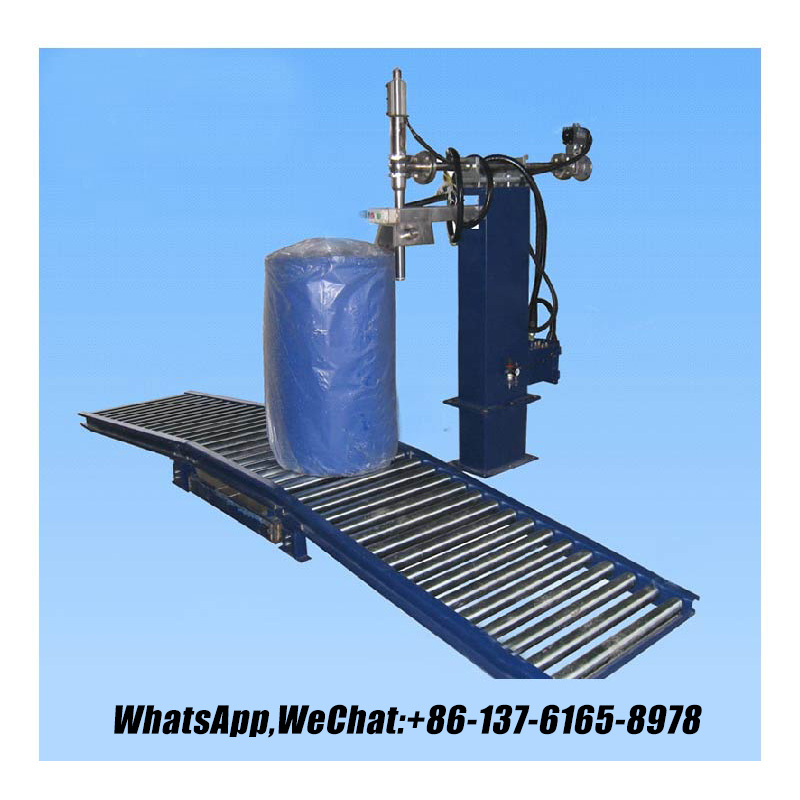
A Multifunctional Filling Machine designed for filling 200L drums of paint and solvents is a versatile, high-capacity solution tailored to handle the unique requirements of these liquids. Below is a detailed overview of its features, benefits, applications, and key considerations:
Key Features:
Precision Filling:
Volumetric or Gravimetric Control: Ensures accurate filling (e.g., ±50ml for 200L drums) using sensors and weighing systems.
Adjustable Filling Speeds: Prevents splashing, foaming, or overfilling, especially for viscous liquids like paint or solvents with varying viscosities.
Material Compatibility:
Corrosion-Resistant Construction: Made from stainless steel (304/316) or chemical-resistant coatings to handle solvents, paints, and other chemicals.
Sealed Hoses and Valves: Prevents leaks and contamination during the filling process.
Versatility:
Paints (water-based, solvent-based, or high-viscosity formulations).
Solvents (e.g., acetone, toluene, ethanol).
Thinners, hardeners, and other ancillary products.
Multiple Liquids Supported: Suitable for filling a wide range of liquids, including:
Customizable Nozzles: Adjustable spouts to accommodate different container sizes and liquid viscosities.
Safety Features:
Emergency Stop Button: Halts operation immediately in case of emergencies.
Overflow Protection: Detects and prevents overfilling to avoid spills.
Fumes Extraction (Optional): Integrated with a fume hood or exhaust system to handle volatile solvents.
Hygienic Design:
Stainless Steel Contact Parts: Easy to clean and maintain, ensuring product purity and preventing cross-contamination.
Drip Trays: Collects spills and drips, keeping the work area clean.
Efficiency:
High Throughput: Capable of filling multiple 200L drums per hour, depending on the product and setup.
Semi-Automatic Operation: Reduces labor costs compared to manual filling while maintaining control over the process.
Customization Options:
Nitrogen Blanketing (Optional): Preserves product freshness by purging oxygen before sealing.
Labeling/Coding Systems: Adds batch numbers, expiration dates, or barcodes to drums.
Conveyor Systems: Automates drum transport to downstream processes like capping or labeling.
User-Friendly Interface:
Touchscreen Controls: Allows operators to set filling parameters, monitor production, and troubleshoot issues easily.
Data Logging: Records filling volumes, batch numbers, and other critical data for traceability.
Benefits:
Precision and Consistency: Accurate filling reduces product waste and ensures uniform fill levels.
Hygiene and Safety: Stainless steel construction and sealed components meet hygiene standards.
Cost-Effective: Semi-automatic operation reduces labor costs compared to manual filling.
Product Integrity: Optional nitrogen blanketing preserves product freshness and prevents oxidation.
Versatility: Suitable for a wide range of liquids and container sizes.
Ease of Use: Simple operation with minimal training required for operators.
Applications:
Paint Manufacturing: Filling water-based, solvent-based, or high-viscosity paints into 200L drums.
Solvent Handling: Packaging industrial solvents (e.g., acetone, toluene, ethanol) for distribution.
Chemical Industries: Filling thinners, hardeners, or other ancillary products into drums.
Coatings and Varnishes: Filling coatings, varnishes, or specialty liquids into drums.
Adhesives and Resins: Packaging high-viscosity adhesives or resins into drums.
Operation Steps:
Drum Placement:
The operator places an empty 200L drum under the filling head using a pallet truck or forklift.
Filling:
The machine measures the required volume or weight of liquid using sensors and fills the drum through a nozzle.
For viscous liquids like paint, a pump or gravity system ensures smooth filling.
Sealing/Capping (Optional):
After filling, the operator manually places a lid or cap on the drum and tightens it securely.
Discharging:
The filled drum is moved to the next stage (e.g., labeling, palletizing) manually or with a conveyor system.
Cleanup:
Drip trays and sealed components minimize spills, keeping the machine and work area clean.
Considerations When Purchasing:
Product Type: Ensure the machine is suitable for your specific liquid (e.g., viscosity, corrosiveness, or volatility).
Output Requirements: Choose a model with the appropriate speed (drums per hour) for your production needs.
Container Compatibility: Verify compatibility with your drums (e.g., size, shape, material).
Hygiene Standards: Check compliance with industry regulations (e.g., FDA, CE, NSF).
Customization Needs: Consider additional features like nitrogen blanketing, coding systems, or integration with other equipment.
Maintenance and Training: Ensure the machine is easy to clean and maintain, and that operators receive proper training.
Budget: Semi-automatic machines are more affordable than fully automatic options but still offer significant efficiency gains over manual filling.
Why Choose This Machine?
This multifunctional filling machine combines precision, safety, and cost-effectiveness, making it ideal for filling 200L drums of paint and solvents. It’s a reliable solution for industries seeking efficient, hygienic, and scalable filling operations without the high cost of full automation. Its versatility allows it to handle a wide range of liquids, ensuring it meets both current and future production needs.
Immediate Order:
Website: http://www.360banjia.cn/product/drumfillingmachines-en.html
China Manufacturing Co Ltd.: https://fillingmachinecn.en.made-in-china.com