Semi-Auto Filling Machine for Filling 200L 84 Disinfectant
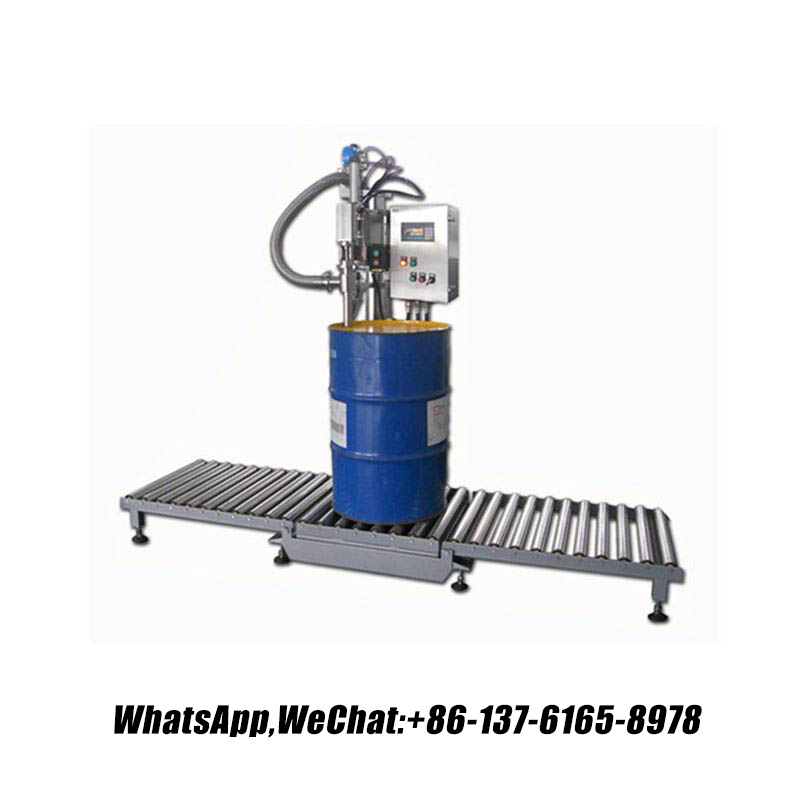
A Semi-Auto Filling Machine for Filling 200L Drums of Disinfectant is designed to handle the precise and efficient filling of large containers like 200-liter drums. This type of machine is ideal for industries such as chemicals, pharmaceuticals, cleaning products, and disinfectants. Below is a detailed overview of its features, benefits, applications, and key considerations:
Key Features:
Semi-Automatic Operation:
Manual Loading/Unloading: The operator places the empty 200L drum under the filling head and starts the process. After filling, the drum is manually moved to the next stage.
Automatic Filling: The machine controls the filling cycle, ensuring accurate volume and minimizing spills.
Precision Filling:
High-Accuracy Sensors: Ensures ±50ml accuracy for 200L drums, reducing product wastage.
Volumetric or Gravimetric Filling: Measures by volume or weight for precise filling, depending on the model.
Adjustable Filling Speeds: Prevents splashing, foaming, or overfilling, especially for viscous liquids like disinfectants.
Disinfectant Compatibility:
Corrosion-Resistant Materials: Constructed with stainless steel (304/316) or chemical-resistant coatings to handle corrosive disinfectants.
Sealed Hoses and Valves: Prevents leaks and contamination during the filling process.
Safety Features:
Emergency Stop Button: Halts operation immediately in case of emergencies.
Overflow Protection: Detects and prevents overfilling to avoid spills.
Fumes Extraction (Optional): Integrated with a fume hood or exhaust system to handle volatile disinfectants.
Hygienic Design:
Stainless Steel Contact Parts: Easy to clean and sanitize, ensuring hygiene and product purity.
Drip Trays: Collects spills and drips, keeping the work area clean.
Versatility:
Multiple Container Sizes: Can handle various container sizes (e.g., 10L, 20L, 200L) with minimal adjustments.
Liquid Compatibility: Suitable for filling disinfectants, chemicals, oils, and other liquids.
Customizable Options:
Nitrogen Blanketing (Optional): Preserves product freshness by purging oxygen before sealing.
Labeling/Coding Systems: Adds batch numbers, expiration dates, or barcodes to drums.
Conveyor Systems: Automates drum transport to downstream processes like capping or labeling.
Efficiency:
High Throughput: Capable of filling multiple drums per hour, depending on the product and setup.
Low Maintenance: Robust design minimizes downtime and reduces operational costs.
Benefits:
Precision and Consistency: Accurate filling reduces product waste and ensures uniform fill levels.
Hygiene and Safety: Stainless steel construction and sealed components meet hygiene standards.
Cost-Effective: Semi-automatic operation reduces labor costs compared to manual filling.
Product Integrity: Optional nitrogen blanketing preserves product freshness and prevents oxidation.
Versatility: Suitable for a wide range of liquids and container sizes.
Ease of Use: Simple operation with minimal training required for operators.
Applications:
Disinfectants and Sanitizers: Filling alcohol-based or chemical disinfectants into 200L drums.
Chemicals and Pharmaceuticals: Packaging liquid chemicals, solvents, or pharmaceutical formulations.
Oil and Lubricants: Filling motor oils, hydraulic fluids, or greases into drums.
Industrial Products: Packaging cleaning agents, adhesives, or industrial fluids.
Water Treatment: Filling treated water or disinfectants into drums for distribution.
Operation Steps:
Drum Placement:
The operator places an empty 200L drum under the filling head using a pallet truck or forklift.
Filling:
The machine measures the required volume or weight of disinfectant using sensors and fills the drum through a nozzle.
For viscous liquids, a pump or gravity system ensures smooth filling.
Sealing/Capping (Optional):
After filling, the operator manually places a lid or cap on the drum and tightens it securely.
Discharging:
The filled drum is moved to the next stage (e.g., labeling, palletizing) manually or with a conveyor system.
Cleanup:
Drip trays and sealed components minimize spills, keeping the machine and work area clean.
Considerations When Purchasing:
Product Type: Ensure the machine is suitable for your specific disinfectant (e.g., viscosity, corrosiveness, or volatility).
Output Requirements: Choose a model with the appropriate speed (drums per hour) for your production needs.
Container Compatibility: Verify compatibility with your drums (e.g., size, shape, material).
Hygiene Standards: Check compliance with industry regulations (e.g., FDA, CE, NSF).
Customization Needs: Consider additional features like nitrogen blanketing, coding systems, or integration with other equipment.
Maintenance and Training: Ensure the machine is easy to clean and maintain, and that operators receive proper training.
Budget: Semi-automatic machines are more affordable than fully automatic options but still offer significant efficiency gains over manual filling.
Why Choose This Machine?
This semi-auto filling machine combines precision, safety, and cost-effectiveness, making it ideal for filling 200L drums of disinfectant. It’s a reliable solution for industries seeking efficient, hygienic, and scalable filling operations without the high cost of full automation.
Immediate Order:
Website: http://www.360banjia.cn/product/drumfillingmachines-en.html
China Manufacturing Co Ltd.: https://fillingmachinecn.en.made-in-china.com